Consumers around the world are becoming more environmentally aware and are placing more and more value on renewable energy sources. This makes heating systems based on wood pellets a huge growth market in the private sector. In Germany alone, one of the largest production locations in the world, production has risen from 1.95 to 3.3 million tons in the past five years.
Environmentally aware customers have long known that good pellet quality is not only convincing in terms of calorific value, but also emits fewer emissions, and they place their trust in well-known certifications in order to find high-quality products. As a result, there is hardly a product on the shelves of large retailers that does not bear a test mark. Now, the applicable standard DIN EN ISO 17225-2 has been updated.
In November 2021, DIN CERTCO, a wholly owned subsidiary of TÜV Rheinland, has published a new certification scheme that meets the updated standard and the changes in the market. Our expert Maximilian Quietzsch explains in an interview which criteria are relevant and how reputable manufacturers can ensure the quality of their pellets.

End customers hardly ever accept wood pellets whose quality has not been confirmed by certification.
Maximilian QuietzschMr. Quietzsch, updating the standard and the certification program was certainly important in such a dynamic growth market and in the current environmental debate. What will change for the manufacturers?
In order to better meet the requirements of end consumers, we have actually slightly tightened the limits in the new certification program. One example is the ash content, i.e. the mass that may remain in the chimney as ash after the cleanest possible combustion. In the future, this may only be 0.6% instead of 0.7% of the original material. The limit value for mechanical strength has also been increased from 97.5% to 98%. This value indicates how much material may rub off during packaging or transport, for example, so that in the end, the customer really buys pellets and not just dust.
Another important change concerns the monitoring of product quality. As the certification is valid for five years, we carry out an annual audit anyway to ensure consistent quality. In the past, if deviations appeared in a sample, we checked this value, controlled corrective measures, and then switched to the regular monitoring rhythm. In the future, manufacturers will be monitored more closely in the event of a deviation. Otherwise, we have clarified some points in the certification scheme that left some room for interpretation in the past.
By the way – our cost structure for certification remains the same! This means that it does not matter how much goods a manufacturer produces in a year.
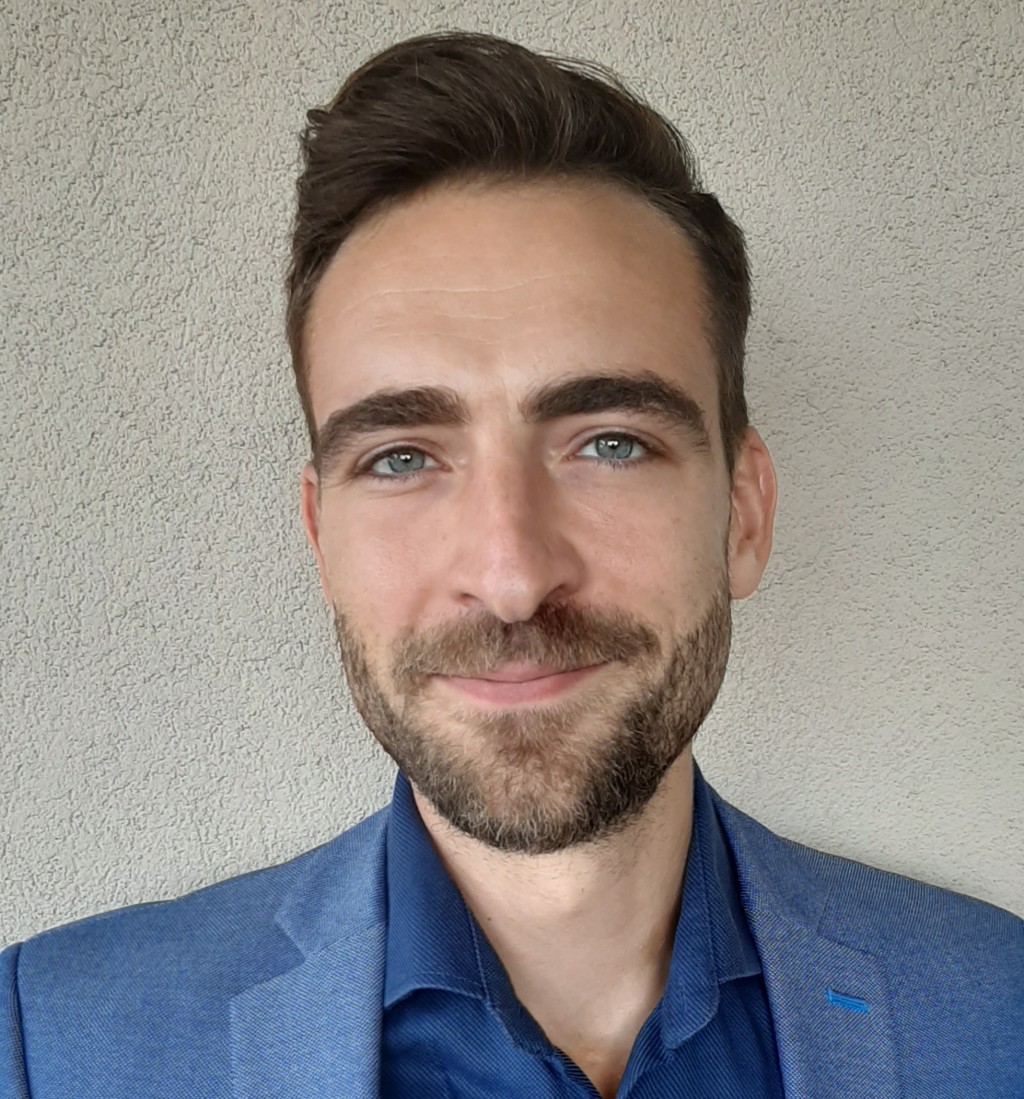
What about "old" certifications? Do they retain their validity?
Correct, these remain in place for the time being. If you have a DINplus certification for wood pellets according to the old certification scheme, the new requirements will be checked within a transitional period of one year in the course of monitoring. So, our customers don't have to worry about that. New customers must of course meet the new requirements directly in order to obtain DINplus certification.
A successful certification certainly also requires a good product. What should manufacturers pay attention to already during production?
The raw material alone is an important factor, although the DINplus certification does not go that far – certifications such as the FSC, which we offer as a combined audit, are more relevant. Other factors are the processing of the material, the mixture and the pressing. As far as quality is concerned, we have been seeing a very positive trend for decades. Without wanting to sound arrogant – we believe that our certification has made a major contribution to this. With DINplus for wood pellets, we launched the first certification of its kind worldwide in 2002, and we have been able to observe a continuous increase in product quality ever since.
This is certainly due in part to pressure from consumers. Anyone who buys a pellet heating system at home is often sensitive to the environmental compatibility of the components. As an auditor, however, I can also cite many good examples where manufacturers see cooperation with us as an opportunity. They actively use the results of their regular tests and documentation for the further development of their products. Many of them attach great importance to calibrating their measuring equipment themselves in order to obtain valid results, and they engage in targeted supplier management in order to improve the quality of their raw materials. The industry is not just a waste recycler, but a highly professional sector of the future.
Since 2018, Maximilian Quietzsch has been Product Manager for fuels and heat pumps and since 2020, he has been Division Manager & Lead Auditor for Wood Pellets at DIN CERTCO. He previously gained extensive experience in EHS management at Siemens AG and General Electric. His expertise is based on his specific academic training. Mr. Quietzsch studied "Environmental Engineering" and "Process, Energy and Environmental Systems Engineering" and was involved in a research project for liquid biomass at the Institute for Bioprocess Engineering at the Technical University of Berlin. At times, he worked as a freelance lecturer at the TÜV Rheinland Academy. |
What are the biggest stumbling blocks in certification? Where do you as an auditor regularly have to complain about deviations?
Conspicuous product samples actually rarely occur, but sometimes they do. Of course, only untreated wood without bark may be used for production, but if it is residual material from a manufacturing process, there may sometimes still be residual substances in the raw material that have to be sorted out. We also determine the content of substances that the tree may have absorbed from the environment during its growth phase. These include chlorine and nitrogen, but also some heavy metals. Strict limits apply to all these substances, of course, which the manufacturers themselves usually keep an eye on.
The documentation or the accompanying documents are more of a challenge. Many manufacturers focus on production and want to make a good product first and foremost. Documenting every step and all deliveries for certification is then sometimes a downstream task. However, we think this is very important, also in the interest of the manufacturers, who should safeguard themselves through documentation. For the labeling of the products, depending on the packaging, there are further strict regulations. An example are the warnings for storage or use, which of course play an important role for the end customer. We naturally check product information on calorific value, fines content, ash content, etc. as part of the certification process, just like the information on traceability.
Finally, the certification must then be correctly identified. In addition to the use of the certification mark, this also includes the registration number. This is where misunderstandings sometimes arise if a manufacturer or retailer wants to market the pellets under several brands. One certification per "brand" applies, not one certification per "manufacturer".
What role do retailers actually play? Can you also acquire certification?
Yes, we basically distinguish between retailers who come into physical contact with the product and those who only operate from their desks, so to speak. Retailers who buy in wood pellets and have them filled in their own facilities are part of the value chain and are also audited during certification.
Large retailers such as DIY stores are usually not involved in these processes at all, but often commission a producer to fill their bags. In this case, they can easily acquire a sub-certificate via the manufacturer so that they can also advertise the certified pellets under their brand.
You just mentioned the "future sector" of wood pellets. How is the market developing? Your assessment?
In addition to the professionalization in the industry, we see above all a great growth in recent years. Germany was the world market leader in production for a long time, and now other countries are following suit. Russia is now on a par with us in terms of production or has even overtaken us. The Europeans, by the way, are grateful customers. In countries such as Italy, Austria, Switzerland, the Czech Republic and the Balkan states, pellet boilers are much more widespread than in Germany. France is considered the strongest DINplus market. So, no wonder that manufacturers from Canada, the USA or Russia want to gain a foothold in Europe.
We think that the environmental debate is likely to be a big driver for wood pellet technology. Pellets are considered carbon neutral because only the carbon that the plants have previously absorbed from the atmosphere is released. Now the aim is to further increase climate compatibility through energy-efficient means of production with little material loss, short transport routes and high quality for clean combustion.
Of course, a big development push also came from the improvement of heating systems. Modern pellet boilers control the supply of material and air through a fine sensor system and thus optimize the heating value. This is also an advantage for customers, who save money as a result. In principle, I would always recommend that end customers inform themselves about the latest technology and the purchase modalities. For every heating system, however, it is important to keep an eye on the entire system. The modern pellet heating system in the basement must therefore also match the radiators in the living area.
By the way, we not only offer DINplus certification for wood pellets, but also for professional storage, transport or the aforementioned pellet boilers. In this way, we want to contribute to an improvement in all areas of technology.
Speaking of transport. How sustainable is heating with wood pellets really?
The origin of the raw material naturally also has a major influence on the carbon footprint of the wood pellets. The original idea was to use untreated waste products from other industries, such as the furniture industry, which is often the case. However, if logs are used, I don't want to demonize that either. By processing it into wood pellets, even logs that could not be used for anything else because of their diameter or growth habit can still be put to good use. However, the most important aspect of sustainable heating with wood pellets remains the transport routes. In the case of wood pellets from Canada and the USA, the transport naturally reduces the environmental balance.
DIN CERTCO has been involved with the topic of wood pellets for a very long time. What can our customers expect in terms of cooperation?
We have spent almost 20 years building up a very extensive partner network of accredited testing laboratories and experienced inspectors. This allows us to carry out DINplus certification for wood pellets worldwide quickly and easily. Nevertheless, we keep all strings in our hands and organize the necessary steps for certification and monitoring in the background. With us, the customer submits an application for certification to DIN CERTCO and we manage the process.
I see another advantage in our online database, where all parties involved can check the authenticity of the certification mark at any time using the registration number. Transparency and trust are very important to us, because this is the basis of the good reputation we have built up in the industry over the years. Incidentally, we are the world's only accredited certifier for the DINplus mark for wood pellets. We are very proud of this.